In just two years, we helped one of our largest growers slash their workers' comp rates. I will review how worker's comp works in Washington, the challenge faced by the grower, and how we, at Harvust, worked with them to accomplish this.
About Harvust's safety tools
Harvust is a labor compliance platform for agriculture, and safety is one of the most important areas. Our agriculture-specific safety tools include:
- Worker training
- Accident log
- Anonymous employee feedback
- Automated hazards communications for high heat and wildfire smoke.
All our safety tools come with automatic time-stamped documentation, so you're prepared for any audit or investigation. It doesn't matter if you are doing the right thing, -- it matters if you can prove it to L&I, BOLI, Cal/OSHA, etc..
About the grower
They are a family farm in WA. They specialize in growing and packing several crops:
- Apples
- Blueberries
- Cherries
- Hops
- Wine grapes
They employ over 1,000 employees at peak season and about 200 during the winter. These employees engage in all kinds of work from office, to field, to shop, to packing, resulting in a diverse set of risks for injury.
Understanding WA workers' comp
The Washington State Department of Labor & Industries (L&I) administers the state's workers' compensation system. Washington requires most employers to participate by purchasing workers' compensation insurance through L&I's State Fund. Premiums are calculated based on the type of work performed, the employer's payroll, and their Experience Factor. The Experience Factor is a numerical value that reflects a company's actual claims history relative to the average claims expected for businesses of similar size and industry. It takes into account the frequency and severity of workers' compensation claims. A factor less than 1.0 indicates a better-than-average safety record with discounted premiums, while a factor greater than 1.0 signifies a higher risk with increased premiums.
The grower's problem: high workers comp rates
Their safety program lacked up-to-date training materials, and structure, leading to wasted resources with costly results. In 2019, their claim costs were above average. Their Experience Factor was 1.11, meaning they were paying 11% more than the standard premium rate for their industry. Based on past claims, this surcharge reflects the higher risk associated with their business. So, to address this the priority is to reduce the number of injuries and the cost of those injuries.
How Harvust helped
In May 2020, we began working with the grower. The first step was integrating their payroll system with Harvust so that we would always have an up-to-date roster of employees. Once their employees were in Harvust, they sent their first training to employees the same day. The setup went quickly because Harvust has a library of over 100 high-quality training presentations, digital handouts, and videos.
We started by replacing their in-person monthly safety meetings with Harvust's direct-to-employee phone-based training. These short, relevant trainings meant that employees' work was not interrupted, resulting in higher productivity and safety engagement. Furthermore, they eliminated paid unproductive time (waiting for the meeting to start, chit-chat, traveling to the meeting site, etc.).
They also utilized Harvust's anonymous safety feedback feature. This allowed them to hear first-hand from workers about hazards (and other issues). With this information, they could prevent accidents caused by problems they didn't know about before.
In 2022, we rolled out 100% Automated Safety Alerts. New WA state regulations (federal is coming soon) mandate that farmers communicate with their workers when the temperature becomes dangerously hot, or the air quality becomes smoky from wildfires. Harvust now monitors the temperature and air quality at their ranches and sends text messages directly to their workers' phones in the field. This communication prevents heat/smoke sickness and creates bullet-proof audit documentation.
The results
In the first two years of using Harvust, their Experience Factor decreased from 1.11 in 2019 to 0.66 in 2021, a 40% reduction! Since then their Experience Factor has fluctuated but has remained below 1, resulting in a sustained reduction in costs compared to their competitors.
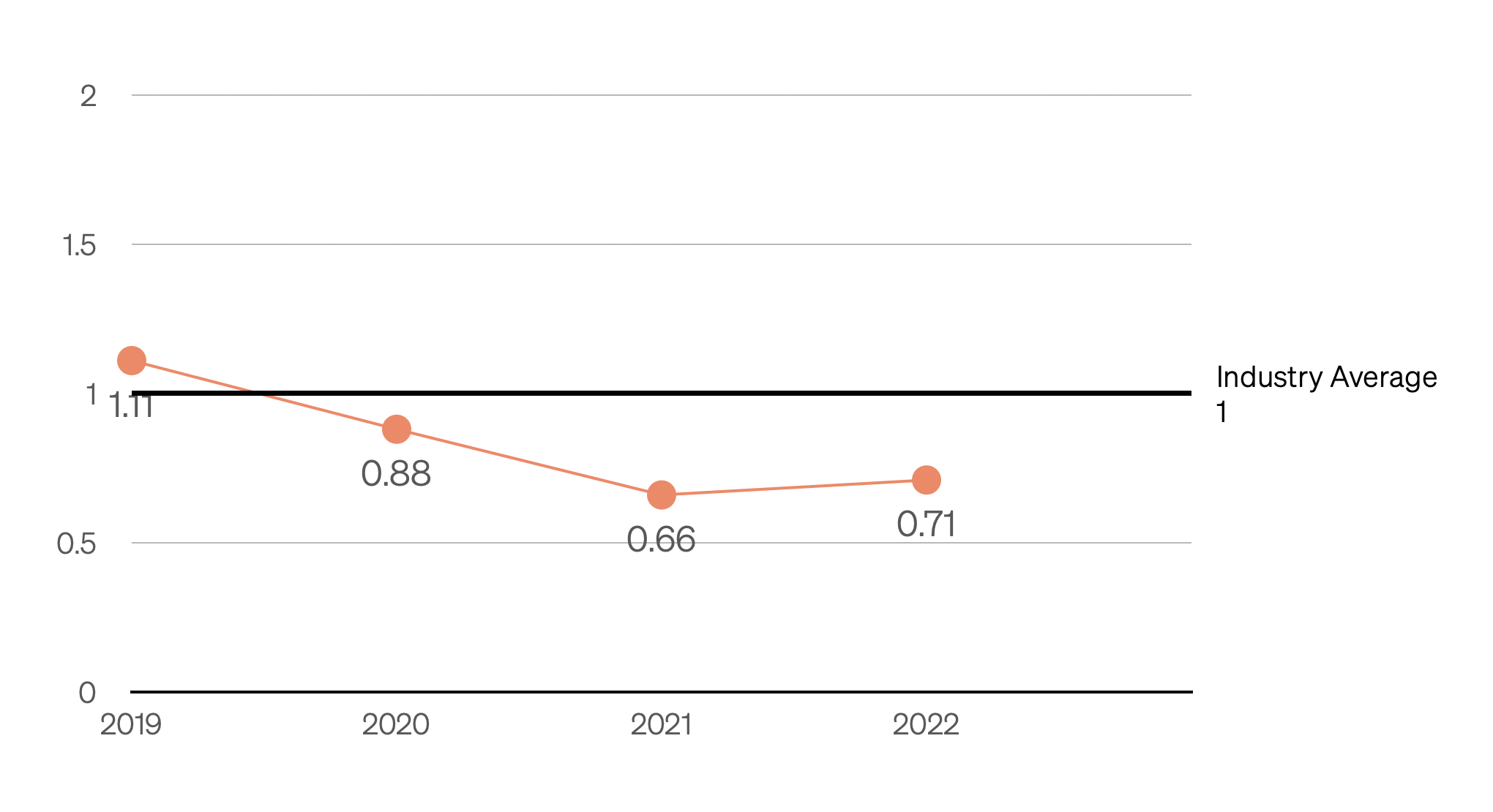
As of July 2024, they use our Automated Dynamic Safety Meetings, which use the data from Harvust's built-in accident log, employee feedback, and other sources to create safety meetings customized to their specific safety needs. Their adoption of Harvust's new safety features ensure the continuation of these significant cost savings.